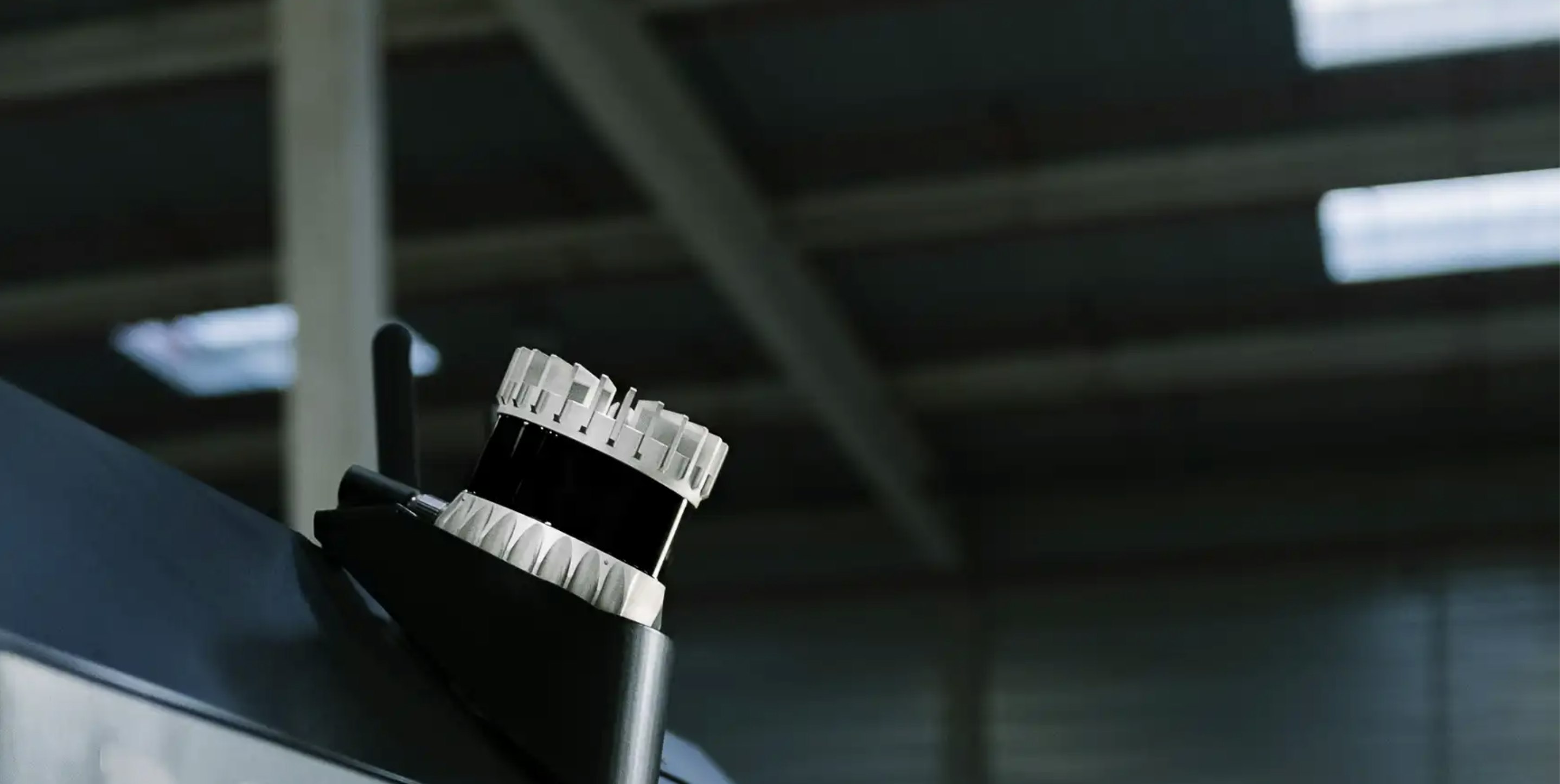
Enhancing Warehouse Safety and Efficiency with Balyo and Ouster
Safety is the focal point of Balyo’s material handling automation business. Their latest platform helps warehousing and logistics companies enhance the safety of their operations and increase efficiency by increasing the object awareness of automated vehicles.
In the fast-paced world of warehousing and material handling, the safety of workers and the efficient movement of goods are two of the most important goals for a logistics manager. With labor shortages and inexperienced staff, it is increasingly difficult to maintain safety standards, especially with the constant drive for faster throughput.
To address these issues, there has been a push to deploy automated forklifts, both fully automated and semi-automated, in an attempt to improve safety and boost efficiency. These advancements have taken the form of driver assistance on manual forklifts, Automated Guided Vehicles (AGVs), and Autonomous Mobile Robots (AMRs). These platforms have partially filled gaps in certain warehouses and slightly enhanced safety, though their adoption and scalability have been limited due to their constrained capabilities, primarily due to inadequate spatial awareness of their embedded sensors.
Most of these systems rely on multiple 2D lidar sensors. Typically, one 2D single-plane lidar is mounted on the bottom of the forklift about 6 inches off the floor to detect low-level objects, such as workers’ ankles. Another 2D lidar is usually positioned as high as possible on the forklift to identify reflectors or waypoints, aiding in localization and navigation within the warehouse. These simple systems address only a very specific subset of safety risks and miss things like rope safety barriers, forklift tines, and low-profile ground objects like empty pallets. Though they are a safety improvement, these systems still have accidents.
Safety is the focal point of Balyo’s material handling automation business. Their latest platform helps warehousing and logistics companies enhance the safety of their operations and increase efficiency by increasing the object awareness of automated vehicles. Leveraging Ouster’s state-of-the-art 3D lidar technology, Balyo has made significant improvements in obstacle detection, navigation accuracy, and startup time for warehouse customers, reducing their accidents and costs of operation.
Enhanced Safety with 3D Lidar
Balyo’s collision avoidance system with Ouster’s 3D lidar, provides their robots with a comprehensive real-time view of the warehouse environment. This system accurately detects the size of objects and people in close proximity to the vehicle. Unlike previous robots that relied on 2D lidar for obstacle detection, Balyo’s 3D-based system can effectively identify stationary and moving objects, including floating objects such as forks on other forklifts. By proactively sensing these potential hazards, accidents, and collisions are prevented, ensuring the safety of personnel and valuable inventory within the bustling warehouse space.
Improved Efficiencies with 3D Navigation
Balyo has also made significant advancements in their navigation system. Previously, their navigation system utilized a 2D lidar that relied on detecting fixed objects in a 2D plane throughout the warehouse. Balyo also used an additional sensor to look for obstacles in front of the robot. However, with the new navigation system powered by Ouster’s 3D sensors, Balyo has eliminated the need for additional sensors on their robots by leveraging the wide field of view of 3D lidar. This not only improves navigation but also reduces the number of sensors required. Unlike traditional systems that depend on 2D lidar and fixed infrastructure, the 3D navigation system does not necessitate additional infrastructure installation in the environment. This simplified installation process reduces costs and enables Balyo’s customers to deploy the system quickly, allowing them to immediately profit from its benefits.
Automation Built for Scale
By harnessing the power of 3D lidar technology, Balyo’s autonomous systems can effectively operate in highly dynamic and complex warehouse environments. With enhanced localization and object detection capabilities, these systems can bring autonomy to narrow aisles, congested areas, and constantly changing warehouses. This flexibility translates into increased efficiency and productivity as the vehicles seamlessly adapt to the ever-changing demands of the warehouse ecosystem.
Balyo and Ouster have joined forces to revolutionize warehouse safety and efficiency. Through the utilization of Ouster’s 3D digital lidar, Balyo has significantly improved obstacle detection, navigation accuracy, and startup efficiency for their warehouse customers. The comprehensive real-time view provided by Ouster’s 3D lidar enables Balyo’s robots to accurately detect objects and people, thereby reducing the risk of accidents and ensuring worker safety. Moreover, the 3D navigation system eliminates the need for additional infrastructure, simplifying the installation process and reducing costs. With improved object detection and localization, Balyo’s autonomous systems operate efficiently in complex warehouse environments.
This innovative partnership between Balyo and Ouster paves the way for a safer and more efficient future in the warehousing industry.