A ship loader is a large machine used for loading materials such as coal, iron ore, bauxite, and alumina onto vessels. Given its large size, there are many blind spots around the vessel, which can lead to collisions that threaten personnel, damage valuable assets, and limit operations.
Existing anti-collision solutions are unreliable
Cameras are commonly used in today’s anti-collision systems but have real limitations. For example, cameras are unable to detect distance and are easily affected by ambient light which results in unreliable data. This requires collision avoidance systems to rely on human judgment to operate in most conditions.
Some companies have tried integrating radar, 2D lidar, or low resolution 3D lidar into their anti-collision solutions, but each of these sensors has drawbacks and does not effectively address the problem. Radar, for example, has low accuracy and 2D or low resolution 3D lidar has very limited resolution and a narrow field of view. As such, more time and additional sensors are needed to scan and generate a reliable map of the area. In both cases, it is extremely hard to monitor a specific area in real-time and the process is inefficient.
In general, these legacy systems are unable to adapt and innovate for future problems.
Ouster lidar helps MRA engineer a safe and reliable ship loading systems
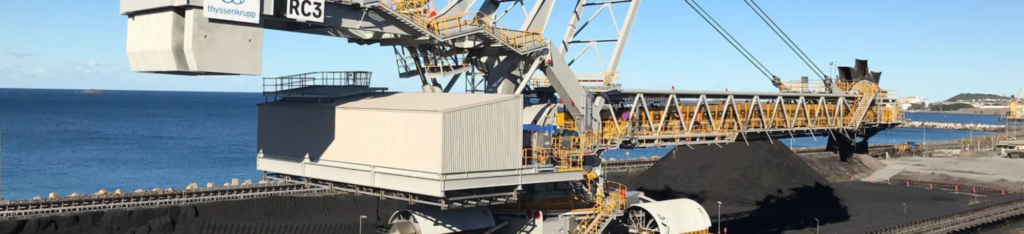
MRA Engineering Australia and QCA Systems Canada teamed up to solve the problem of
legacy anti-collision systems using Ouster lidar sensors for this Ship Loader Anti-Collision
System (SLAC) in the Port of MetroVancouver; the 3 rd largest Port in North America and
critical part of the Canadian economy.
MRA and QCA are both engineering companies with experience using multiple sensing
technologies, including radar and lidar, across product offerings: ship loaders, vessel anti-
collision systems, smart 3D stockyard modeling, and train load out and dump station
automation systems. Ouster was selected for this application for the quality and
performance of its lidar sensors, in addition to value the technology brings to its systems.
“Historically in lidar versus radar debates, lidar provides better accuracy while radar is thought to have improved environmental noise performance. Through testing, we have found Ouster lidar to have inherently excellent performance across a wide-spectrum of environments when augmented with our application specific proprietary filtering algorithms. This has helped us deliver a superior solution for accuracy and environmental robustness,” MRA stated.
Building a reliable 3D map with digital lidar
The MRA-QCA system uses millions of data points from Ouster sensors installed on the ship loader to build a 3D map of the loader and vessel alongside the wharf. The model is created and updated in real-time as the ship loader changes position. Overlapping data points and perspectives create a highly accurate and reliable model with the distance of each machine part to the vessel continuously calculated as well.
MRA uses the OS1-32 for its high-resolution and wide field of view (360H x 45V), which helps build the 3D map in real-time, reduces blind spots, and significantly increases the system’s productivity.

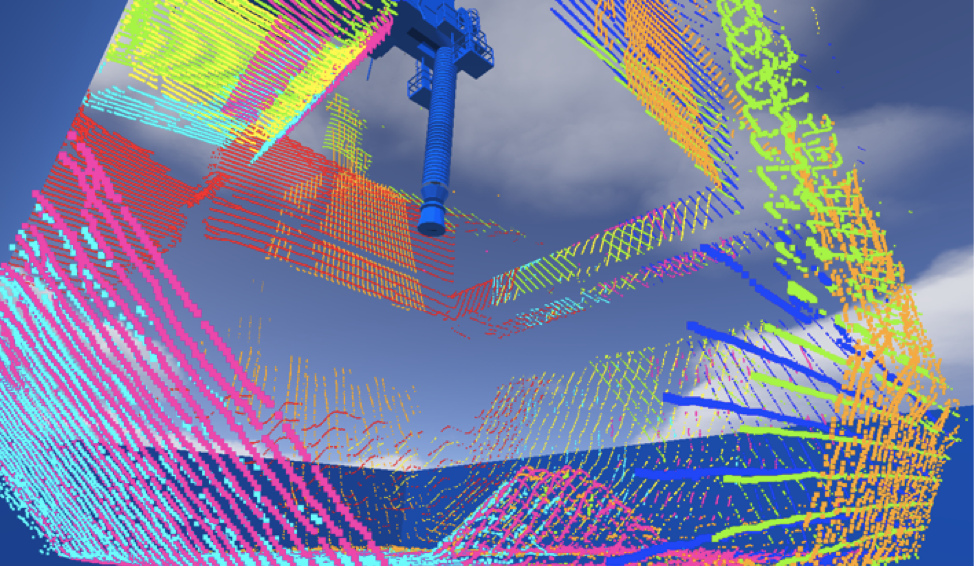
Calculating the available clearance to navigate narrow spaces
Based on real time 3D mapping, the SLAC system is able to calculate the available clearance between the ship loader and the vessel. The calculation takes into account the complex shapes and distance, communicating with the control system to automatically slow and adjust as the ship loader approaches the vessel.
Comprehensive coverage in all-weather conditions
In addition to the movement of the ship loader and vessel, there are also unpredictable environmental factors to consider such as sea swell, tide, and wake from passing vessels. Leveraging the 3D mapping built with Ouster lidar, MRA’s SLAC works with all major vessel classes, bridge configurations, and hatch types in both harbors as well as open ports. The system has also been tested for reliability in heavy rain, snow, fog, and dusty conditions.
“We have been very happy to date with the performance of the Ouster lidar. Prior to selection, Ouster lidar was placed through rigorous internal suitability testing, including accuracy, resilience to environmental noise, and harsh environmental conditions such as those experienced on ship loaders.”
Interested in learning more about Ouster digital lidar or the MRA anti-collision solution? Contact our sales team.
You can learn more about MRA and QCA on their websites: