Ati Motors’ autonomous mobile robots (AMRs) go beyond the manufacturing floor and add new use cases in warehousing and outdoor material movement.
Material movement is an essential part of lean process thinking. Customers want to automate such tasks; however, the existing generation of 2D lidar-based robots have a number of drawbacks: including time and resources required to operationalize the system and performance gaps that reduce productivity. More performant and more reliable systems are required to solve these drawbacks. This is where 3D digital lidar comes in, helping companies like Ati Motors achieve new levels of automation in warehouses and outdoor distribution yards.
Where is the friction?
The first generation of industrial robots developed to improve efficiency were automated guided vehicles (AGVs). While AGVs went a long way in terms of increasing productivity, they also had a significant drawback. AGVs required a fixed route and special infrastructure to guide their movements, making them ill-fit for dynamic warehouse and manufacturing environments.
The need for efficiency and flexibility drove the innovation and the development of autonomous mobile robots (AMRs).
However, the growing AMR industry has faced two primary challenges: operation in legacy environments and long integration roadmaps.
The first iterations of AMRs implemented 2D lidar for localization and flexible routing, but they relied on similar legacy platforms as AGVs that utilize wheel encoders to track the odometry of the vehicle and monitor its location and trajectory. These systems are accurate only when they are operating on smooth controlled surfaces that prevent any mechanical ‘slippage’ in the wheels. This requirement turns out to be a big limitation to the AMRs and prevents them from operating effectively outdoors or on uneven warehouse floors.
Building their system from the ground up with 3D digital lidar, Ati is able to overcome these limitations. 3D lidar sensors allow their vehicles to detect objects from floor to ceiling while also monitoring the vehicles odometry – without the need for legacy wheel encoders. This has enabled Ati to operate indoors as well as outdoors, regardless of the surface or environment.
In addition to all-surface observation, Ati is able to leverage 3D digital lidar to detect obstacles on the ground such as oil patches, chipped floors, ramps, and drop-offs.
Ati Motors: designed to leverage the power of 3D with Ouster digital lidar.
Ati Motors flagship vehicles, the Sherpa Tug and the Sherpa RollerTop, were created with these problems in mind. Sherpas safely, reliably, and efficiently move trolleys and totes with payloads of up to 1 ton, without human intervention or remote oversight, over difficult terrain, adapting themselves to the existing environment. As opposed to a common approach in the market to add new sensors on top of existing platforms, Ati Motor’s vehicles are designed from first principles, ground up, to achieve these objectives and unlock the potential for a new age of autonomy.
Ati’s robots integrate with existing trolleys and conveyor systems and can therefore be incorporated into workflows without any alterations to infrastructure. Their design includes significant safety, localization, and deployment considerations, allowing the Tug to tackle ramps and move between a factory floor and outdoor spaces with ease.
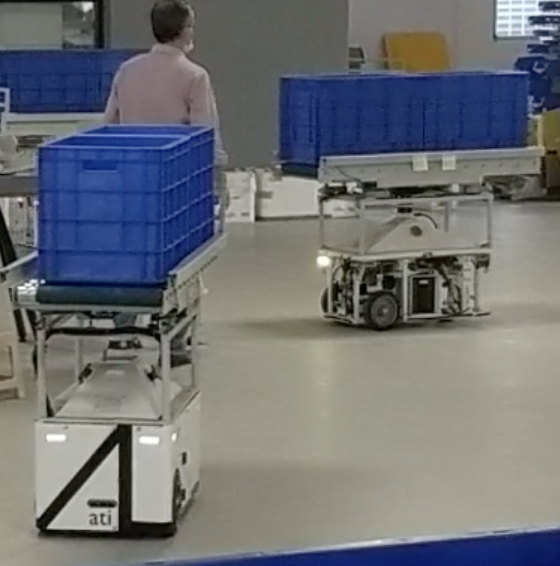
Sherpa RollerTop carries bins to augment pick-and-place processes by delivering materials to workers at workstations within the factory or warehouse. It is particularly useful for electronic assembly plants and e-commerce fulfillment centers.
Leveraging machine learning and integrating 3D digital lidar, Ati Motors has been able to overcome both integration complexity and the challenges of operation in legacy environments. Ati Motor’s bots can be operational in a factory or warehouse in as little as one workday, with no changes to infrastructure.
Ouster’s digital lidar is built for reliability in rugged operating environments
Ouster’s products undergo rigorous shock and vibration testing before leaving the factory, so they are a perfect match for Ati Motors’ key ruggedness requirements: the ability to operate in a variety of outdoor unpaved environments and to navigate ramps and bumps robustly and handle inclement weather.
Powered by its new L2X chip and based on its unique optical design, Ouster’s digital lidar is less affected by rain, snow, and dust that can obscure the lidar window. By processing both the strongest and second strongest returns of incoming light, the sensors accurately detect objects that are partially obstructed behind external elements such as dust, smoke, rain, or fog, or even behind thin, delicate objects like a wired fence.
All Ouster lidars are designed to IP68/69K standards, reliably performing across unpredictable weather conditions and extended outdoor use. As a result of significant performance improvements over the past year, Ouster implemented a standard 2-year warranty in February 2021.
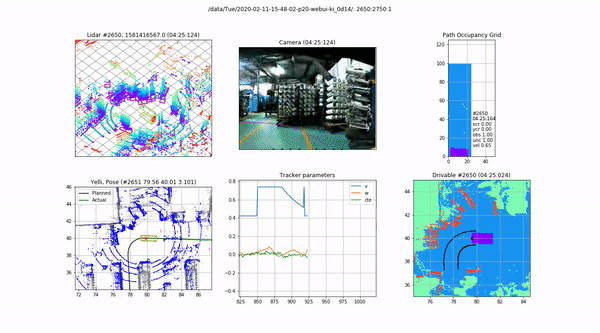
Together, Ouster and Ati Motors are bringing new levels of automation to material handling, improving customers operations across the supply chain.
“One key advantage Ouster’s sensor has brought to us is the ability to localize indoors and outdoors, in all weather conditions, with great precision, expanding the kinds of environments in which the vehicle can effectively operate,” said Saurabh Chandra, CEO at Ati Motors.
Ati Motors has customers in industries as wide ranging as e-commerce, consumer goods manufacturing, automotive and pharmaceuticals, so the ability to seamlessly integrate in a variety of environments is essential.