Founded to address expensive, inefficient, outdated or nonexistent solutions to volume measurement, condition monitoring, and surveillance in raw material processing, Flasheye uses Ouster 3D digital lidar to increase both the safety and efficiency of industrial worksites through their smart monitoring system and interface.
Traditional solutions for monitoring material processing are unreliable and costly
Raw material processing involves moving and handling massive amounts of stock in environmentally challenging scenarios. While a number of solutions attempt to address this problem, they are often unreliable and costly. Material processing worksites primarily function outdoors in a broad spectrum of climate conditions subject to dust, intense vibration and shock. This can often lead to halts in production resulting in losses of hundreds of thousands of dollars each hour that the equipment is offline. Industrial sites regularly invest in equipment to monitor operations and reduce stoppages that can lead to significant savings in operating expenditures.
However, the cost is perhaps the most prohibitive drawback to the universal adoption of these systems as expensive solutions are impractical for wide deployment and often limited to only the most critical areas of specific worksites. This leaves large opportunities for further gains in cost savings, efficiency, and safety.
How are we doing it now?
Currently, the most common method of material monitoring on raw material worksites is either manual oversight or one-dimensional systems of measurement. For example, conveyor belts processing raw minerals may be manually monitored for deviations and spillage with human oversight, but this limits production to labor availability. Laser and 2d lidar measurement solutions have been used in certain circumstances, but often prove unreliable in outdoor environments due to dusty conditions. Ouster’s 3d lidar, conversely, provides additional data layers, such as calibrated reflectivity, to help separate dust and other obscurants from the material being measured.
Video-based solutions similarly fail the environmental demands, faltering in conditions that are either too hot, too cold, too dusty, too dark, or too bright. In other words, almost every condition that exists on a material handling worksite. Other tools succeed in measuring temperature, speed or the vibration of conveyor belts, but each system exists independently and provides an incomplete picture.
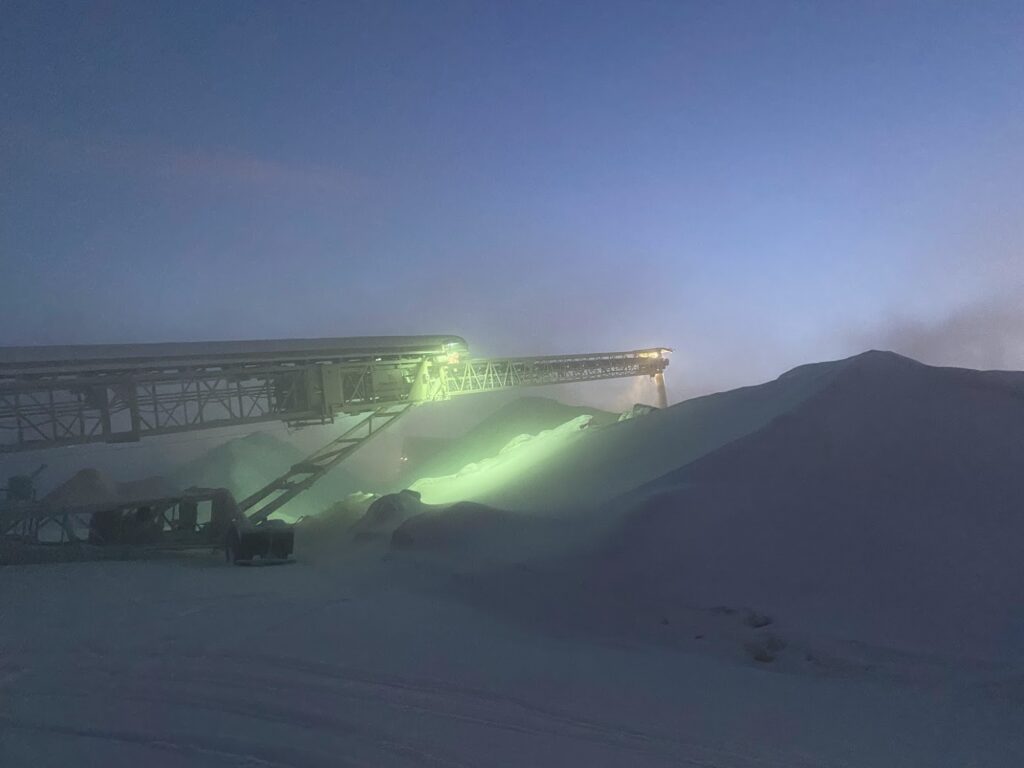
Leveraging 3D digital lidar for comprehensive worksite monitoring with Flasheye
Flasheye’s 3D lidar-based worksite monitoring and surveillance solution is optimized for industrial environments and, aside from its volumetric measurement applications, is additionally used to monitor material processing operations and improve workplace safety. With a ruggedized edgebox and user friendly configuration interface built for reliable 24/7 operation, Flasheye improves efficiency and safety at a price point that will allow site-wide monitoring on a single system, where previously this would have required a collection of expensive and disparate tools.
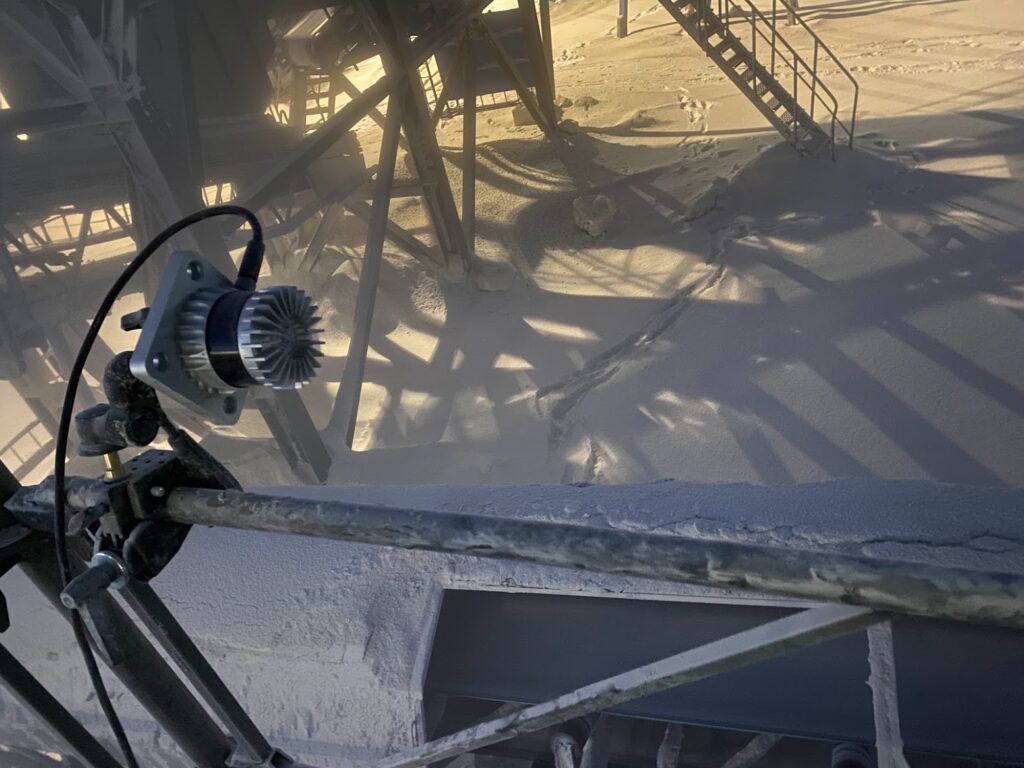
Flasheye relies on an Ouster OS1 sensor for its durability, reliability, and wide field-of-view. Its customers are looking for an extremely dependable system with low failure rates. Ouster’s digital lidar stood out for its robustness and applicability across diverse sites and scenarios.
“Customers want it to actually work, so we chose Ouster”
– Flasheye COO, Ida Rehnström
Optimizing resources and productivity
Efficient and sustainable systems are key for Flasheye in order to ensure no resources are wasted.
Ouster’s digital lidar outputs highly reliable 3D data, even in adverse conditions, which enables Flasheye to employ material measurement tools across an entire worksite, rather than select locations. The lidar sensor can detect side movements of the conveyor belt, indicating there is a risk for damage or breakdown. Inventories can be optimized through volumetric detection, limiting the need for manual belt scales. Early ascertainment of spillage, for example, can prevent wasted product that must be re-processed as well as stoppages in the operation.
Increasing safety
Another key use-case for the Flasheye solution is workplace safety. The sensor’s wide field-of-view allows for volumetric surveillance in multiple zones around the conveyor area. End users can set restricted areas, automatically control actions on the ground, and set rules for different zones. This can include limiting vehicle or personnel access during certain times, designating safety zones, opening up escape routes in case of emergencies, and detecting intrusions. Moreover, spillages and leaks of potentially hazardous materials are spotted from an early stage and are therefore preventable – and if a spillage is detected by the Flasheye solution, a worksite alert can be issued to prevent personnel from entering high risk danger zones.
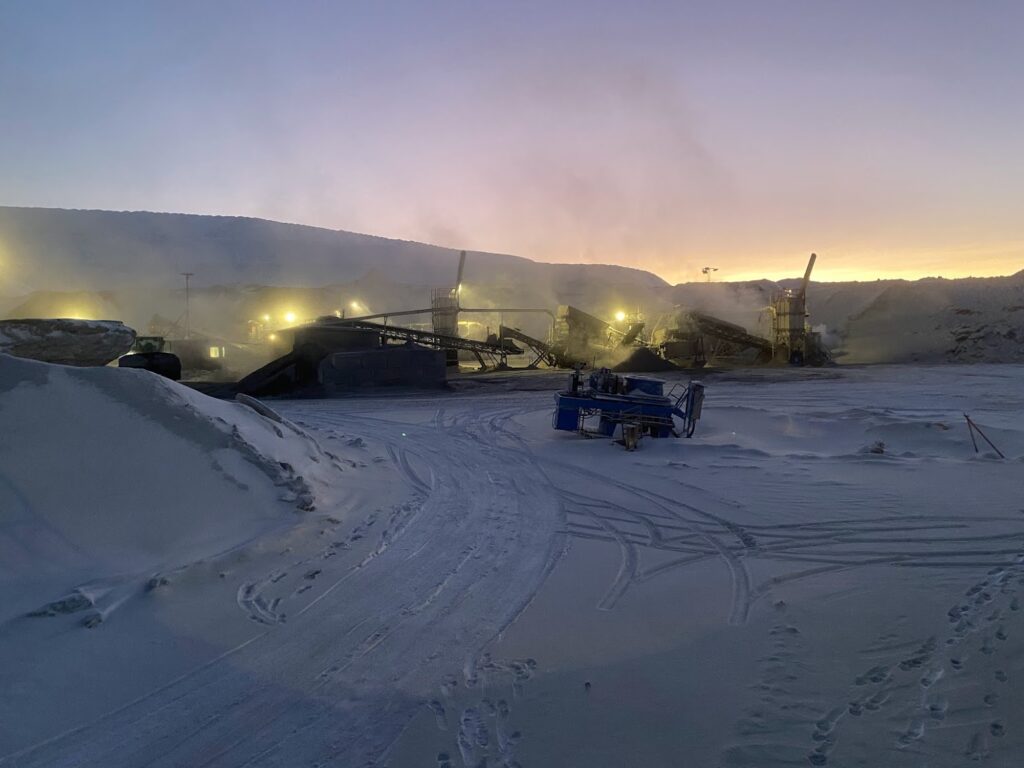
We’re excited to watch Flasheye transform the world of raw material handling. To learn more about their team and offerings, visit them at www.flasheye.se. To learn more about Ouster and its industrial applications, reach out to our team!