When sourcing components for automotive production, OEMs seek high-performance, affordable, and reliable parts that can be manufactured dependably in mass quantities. This is true of every aspect of a vehicle and it is no different for lidar. When it comes to cost, reliability, and manufacturability it’s pretty intuitive; fewer moving parts means fewer fragile components that can break or need calibration and building sensors becomes simpler and more economical. The obvious choice for cost, reliability, and manufacturability is solid-state lidar – a sensor with a simple design and no moving parts that delivers the performance that OEMs need for autonomous driving features.
There is agreement across the auto industry that a true solid-state flash architecture is the end state for automotive lidar. As a stopgap solution to try and win OEM deals, many lidar companies are deceptively marketing “solid-state” architectures that leverage mechanically scanning mirrors. In a rush to bring vehicle automation to market, OEMs have been forced to settle for these scanning, non-solid-state lidar sensors that are expensive, unreliable, and difficult to manufacture, when true solid-state lidar is just around the corner.
Watch out for the lidar scan artists
Any mechanical scanning requires moving parts. Calling these systems “solid-state” has stripped the term itself of any meaning and has flooded the market with skepticism and distrust.
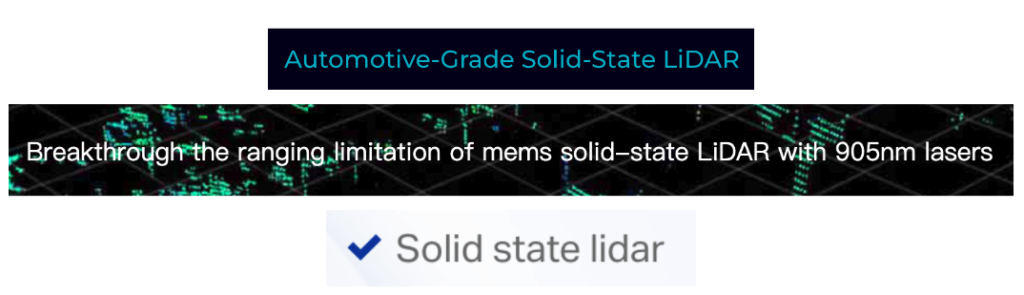
In recent years, the lidar industry has attempted to cover up the inherent disadvantages of mechanically scanning by using the term “solid-state” liberally (and incorrectly). Dating back to 2016, one lidar provider dubbed its spinning analog lidar sensors as “solid-state hybrid”. Others use the “hybrid” designation to refer to their non-spinning, but still mechanical scanning lidar. Even worse, there are many who claim solid-state without even using the term “hybrid”. A Forbes article addressing various scanning mechanisms stated that “One of the key differentiating features of the various solid-state solutions is the laser beam steering mechanism. The most commonly used approach is micro-electro-mechanical-systems (MEMS) which effectively uses microscopic mirrors on a chip to direct the laser pulses across the sensor’s field of view.” In reality, there are only two types of lidar: lidar with no moving parts and lidar with moving parts.
Hybrid technology is rarely the desired end state, but merely a temporary compromise to meet a near-term goal. The hybrid electric vehicle (HEV), as an example, makes significant compromises on multiple fronts (performance, cost, complexity) to accomplish its goal of improving city fuel efficiency. The coming proliferation of battery electric vehicles that are affordable and meet the range requirements of consumers will inevitably make HEVs obsolete. We see many of the same patterns when looking at the lidar industry today. Automakers have waited patiently for lidar to become affordable, reliable, and scalable for years, and they know that can only be accomplished with a truly solid-state architecture.

So was Elon right? If automakers are stuck with moving parts in their lidar sensors, then yes, lidar is doomed for consumer ADAS applications. Let’s take a deeper look at why.
The future is the true solid-state sensor suite
There is nearly unanimous agreement across global OEMs that lidar is an essential component to enable safe L2 – L5 automated driving. However, fitting lidar into the OEM requirements has proven to be much easier said than done. Carmakers need lidar suppliers to provide what camera and radar suppliers have been delivering for years. There are four non-negotiable criteria to the success of lidar in high-volume automotive programs:

Compromising any one of these would prove fatal for the commercial success of a next-generation vehicle platform. Modern automotive cameras and radar sensors fit the requirements of high performance, reliability, and ease of manufacturing because they are digital, true solid-state technologies.
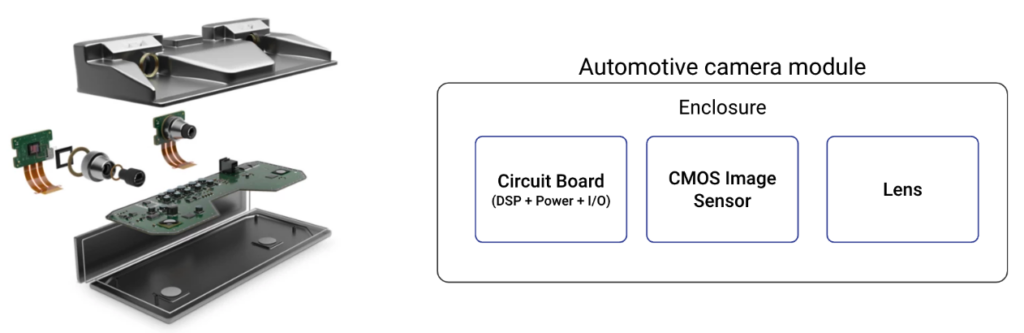
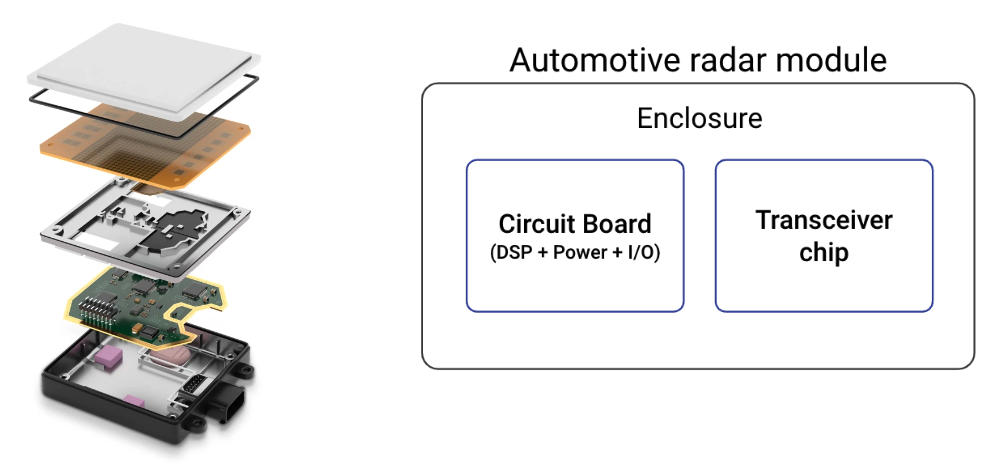
Carmakers can stop settling
One thing is clear when looking at the lidar market today: solid-state matters. The scan artists in the industry are proposing non-solid-state solutions to OEMs that may work for development projects, but will inevitably fail in the transition to mass production. Carmakers should not be forced to settle and waste valuable R&D resources on temporary solutions when true solid-state lidar is the only viable path forward to deliver safe and affordable automated driving to the masses.
Reach out to our team to learn about Digital Flash: our true solid-state platform that is the end-state of automotive lidar.