Spinning lidar sensors have many benefits, but physical robustness hasn’t historically been one of them. Ouster changes that.
Spinning lidar sensors have a lot going for them, which is why Ouster’s first product spins. They can see in 360° so a single sensor can perform the work of four or more fixed field-of-view sensors. They produce data in a format that roboticists have become familiar with over the last ten years, and if you want to scan – which the majority of lidars do – rotary motion is an incredibly efficient method compared to galvos and even MEMS. They also allow for producing structured lidar data, in both 2D and 3D.
But there is also a conception that spinning lidars are by definition big, heavy, power hungry, expensive, and unreliable. Looking at the market, it’s clear why – nearly all spinning lidars are big, heavy, power hungry, expensive, and unreliable.
We knew that in order for the OS1 to succeed, we had to confront the expectations surrounding spinning lidar. The OS1 couldn’t just be a good design – it had to be better engineered in every way, and I think we’ve achieved that with the OS1 being the smallest, lightest, most power efficient, and most affordable high performance lidar on the market – solid state or otherwise.
What we haven’t spoken about as publicly is how we’ve engineered the OS1 to an extreme level of robustness and reliability. Due to its simpler architecture, small number of discrete components, and all-silicon design, the OS1 is a remarkably rugged device.
Quality and reliability testing is a big focus at Ouster, and as with most things, we’re only as good as the team that’s doing the work. In this case, we’re lucky to have a group of veterans from the solar industry who’ve spent their careers making 25 year warranties the norm. Over the past year, they’ve tested the OS1 in a broad array of conditions as part of a structured quality and reliability engineering design and validation process.
Even though we’re still in the middle of this work, the OS1 is on track to be to be the most reliable, most durable 3D lidar on the market according to a host of the most stringent automotive, industrial, military, and other physical stress standards.
Shock Tests
In the real world, doors slam, potholes don’t get fixed, and sometimes your drone doesn’t make a perfect landing. The OS1 has passed multiple variations of the following shock tests and already exceeded automotive standards like the GMW3172 General Motors reliability specifications:
- Mechanical Shock (Pothole): 25g
- Mechanical Shock (Closure Slam): 40g
- Mechanical Shock (Collision): 100g
All of these tests consisted of hundreds, or in some cases thousands, of shocks in various orientations. The standardized test methods (such as IEC 60068-2-27) leave no room for cutting corners – they are designed to simulate the shock that a vehicle experiences on a daily basis, over many years of real-world deployment.
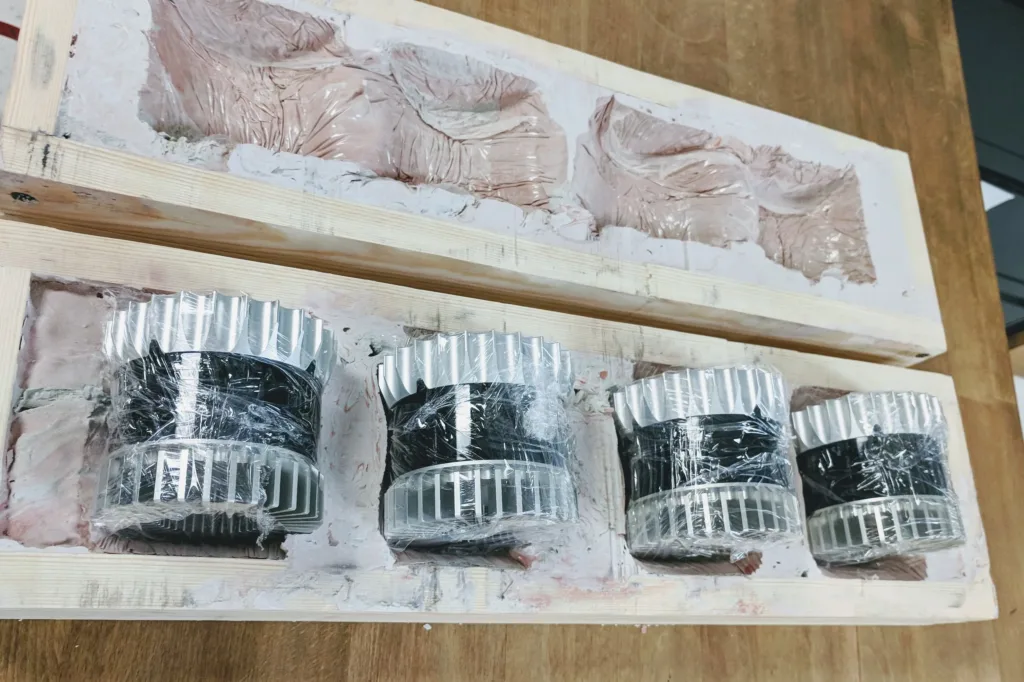
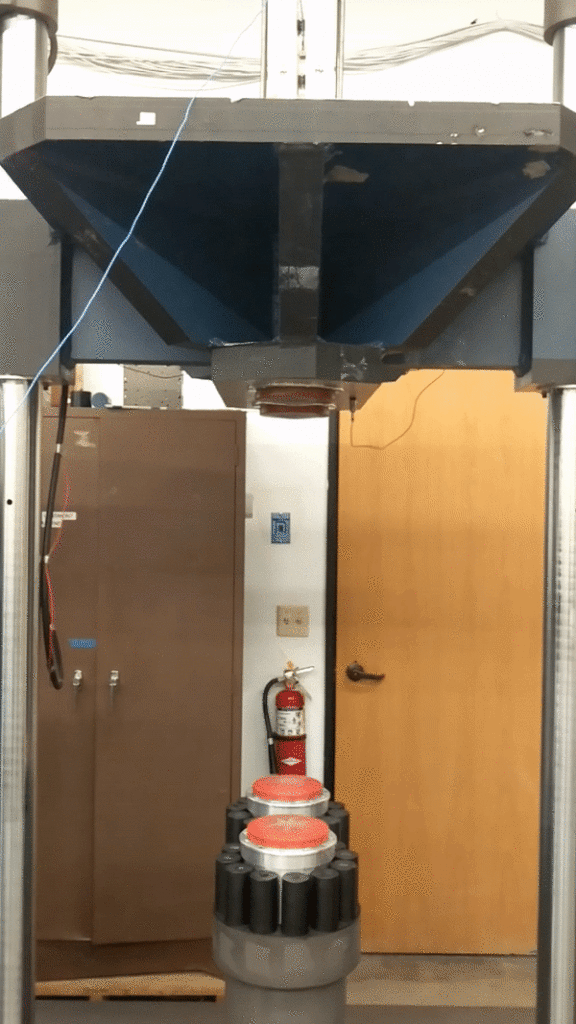
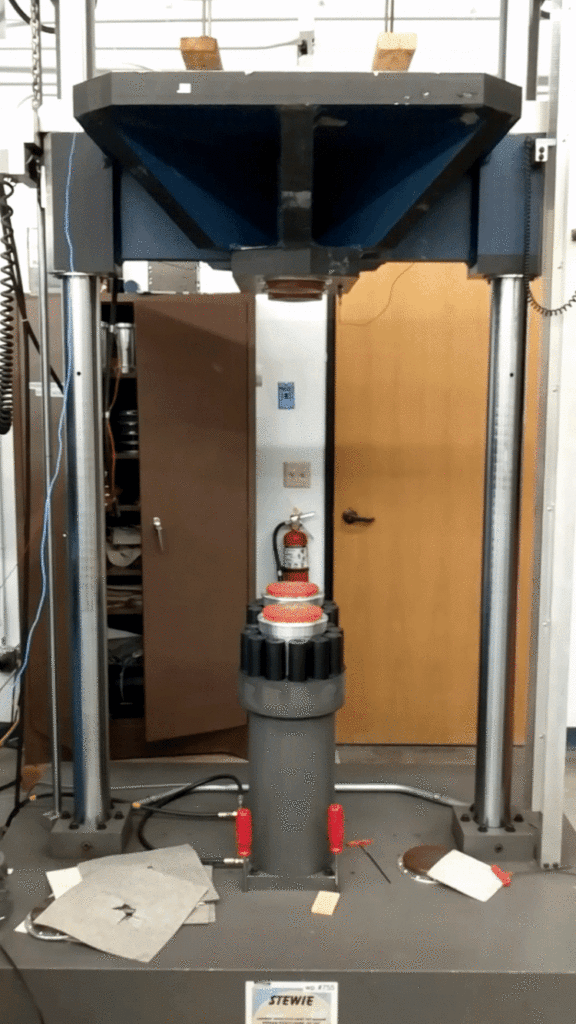
Vibration Tests
Sensors also need to survive long-term vibration. Not all roads are well paved, and in many industrial settings and otherwise, sensors are mounted on equipment that has significant vibration as part of its normal operation.
In this category, we’ve cleared a high bar, passing tests of 3g rms, performing at or above both the General Motors and major German automaker specifications for vibration. We don’t just ensure with all these tests that the sensors operate – we thoroughly evaluate them to ensure that they experienced no degradation in performance at all.
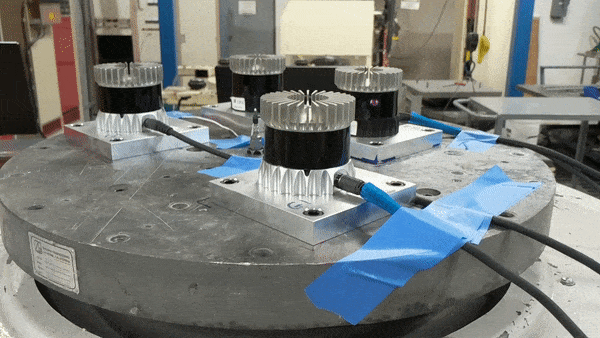
Underway: UV Exposure
Ouster sensors are designed to be in the field, in constant operation, for years at a time. That means lots of UV exposure. The OS1 is currently undergoing an accelerated UV exposure test of several thousand hours, representing 10 years of sun exposure in the field. We’re also working on real-world UV testing outdoors in Arizona. As you might imagine, these tests take some time, and we’ll report back once they are finished.
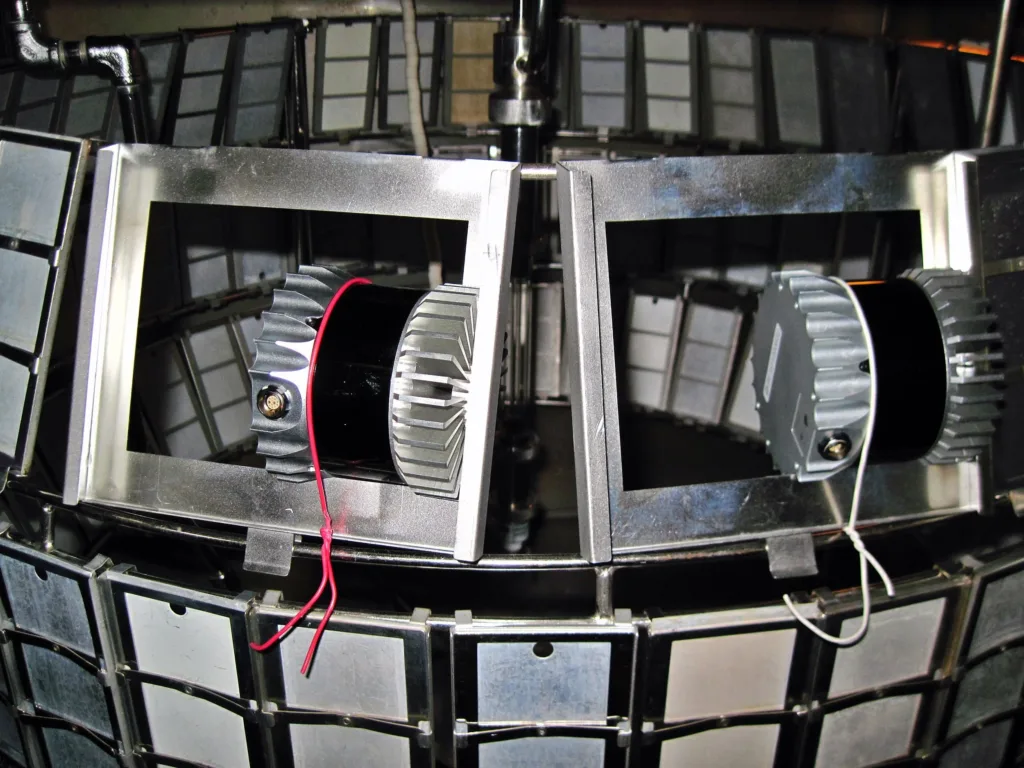
… And more to come
Reliability and durability are just two components of Ouster’s testing program for our sensors, but since spinning lidar has gotten a bad rap, we wanted to cover these areas first. Look for future updates on functional safety (ISO 26262), performance in various weather conditions, optical window obscurance, water incursion, humidity handling, and other general abuse.