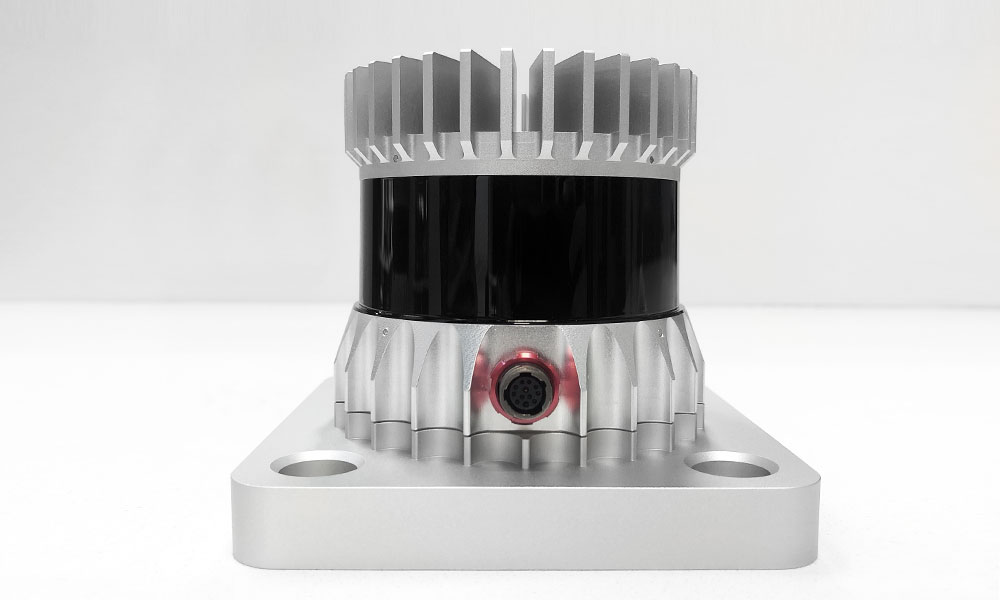
Spinning lidar doesn’t need to be unreliable
Ouster sensors are designed to be highly reliable in the field. We’ve already told you how our Multi-Beam Flash Lidar technology has a simple architecture – with a 100x reduction in component count vs legacy lidar sensors, we’ve eliminated hundreds of points of failure. We’ve demonstrated the durability and reliability of this simple design in these test results.
Today, after 9 months of development, we’re introducing an upgraded window seal and new connectors and cables to meet automotive-grade quality requirements and increase our sensors’ ingress protection rating to IP69K from IP68.
Rocket-style connectors
To achieve automotive-grade reliability for our customers, we’ve switched from our previous push-pull connectors to custom-designed bayonet connectors that secure the cable to the sensor.
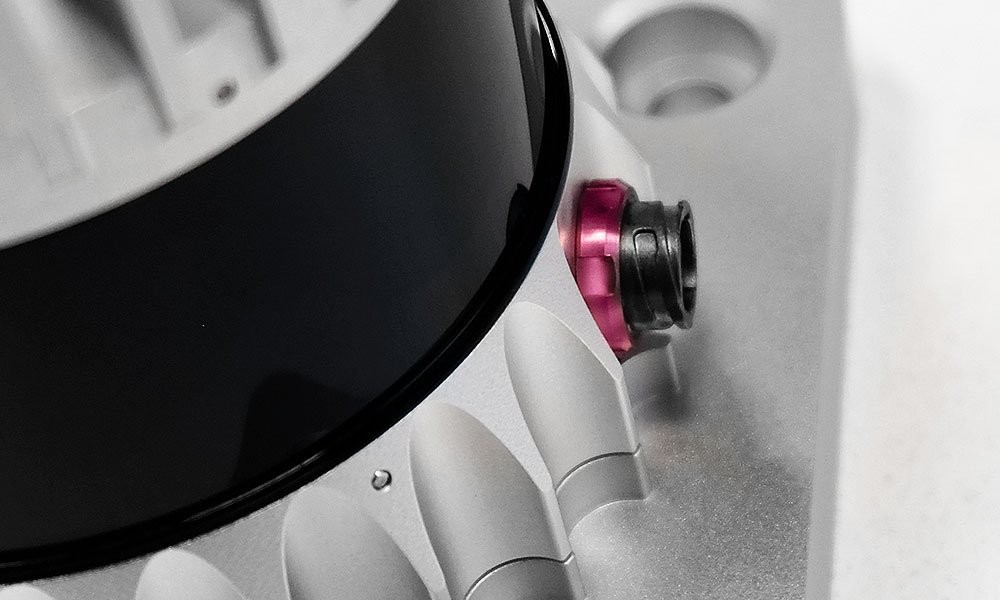
Bayonet connectors are so secure that they’re used in aerospace applications. You would never see a push-pull connector on a rocket!
The highest IP rating in the industry, and aiming higher
IP ratings are internationally recognized classifications of protection against water, dust, and intrusion. As part of the rigorous testing protocol, products are run through a series of water submersions, high pressure washes, and similar tests for dust and particulates.
As an initial test, we put a few connected sensors through this protocol; all sensors survived our battery of tests and came out fully functioning. We sent batches of these sensors out to certified testing facilities, and are expecting to get our official certification soon. These tests will bring our IP rating up to IP69K, making our lidar the highest rated sensor in the automotive lidar market.
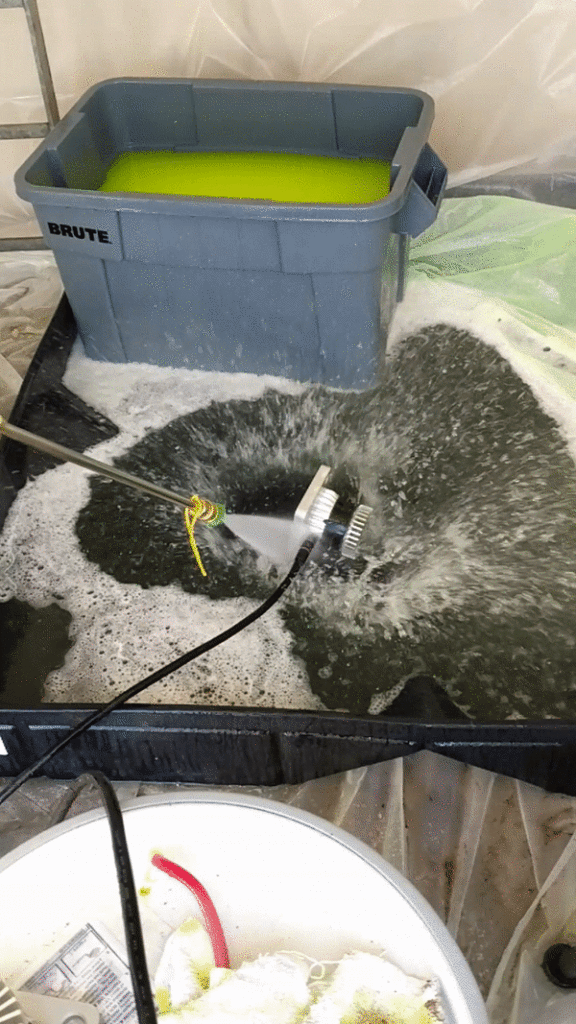
This new rating will certify that the OS1 is resistant to high temperature (80oC) and high pressure (1160-1450 PSI) washing, plus water submersions of up to 1.5m for thirty minutes.
So next time you drop your lidar sensor in water, your car goes through the car wash, your drone flies into a river, or your robot walks into a massive puddle (or a water fountain in a mall), you won’t need to worry about your lidar sensor.
We’ll continue to put our sensors through challenging tests until we achieve full automotive grade certification, so look out for future updates on what other abuse our sensors can handle!
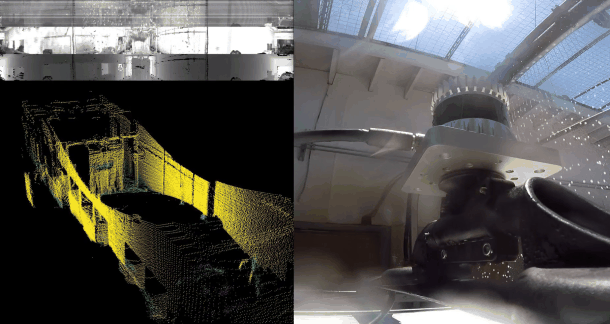
Giving you options
Over the past year of shipping sensors to over 400 customers, we’ve learned that with cables and connectors, one size does not fit all. Your projects require different cable grades and different connector angles, so this update incorporates that feedback with a variety of new options.
We now have different cable lengths, thickness, and connector angles, meant for every application and every integration, so you can customize cables to best fit your platform.
The new cables and connectors are available in the following options:
[A] Cable Lengths: 1m, 2m, 5m, 10m, 15m, and longer by request
[B] Cable Thickness: 22 AWG power, 28 AWG signal or 26 AWG signal
[C] Connector: straight, right angle
Our new thick 26 AWG cables are meant for automotive applications – they are standardized UL-758 and specifically designed for automotive-grade requirements. These cables can withstand heat and water pressure, and maintain performance up to 40m, giving you more flexibility when running cables. The tradeoff with these rugged cables is that they are stiffer and have a larger 8cm bend radius. The other option, the thin 28 AWG cables, are similar to our current cables and have a tighter 4cm bend radius, making them ideal for robotics and drone platforms.
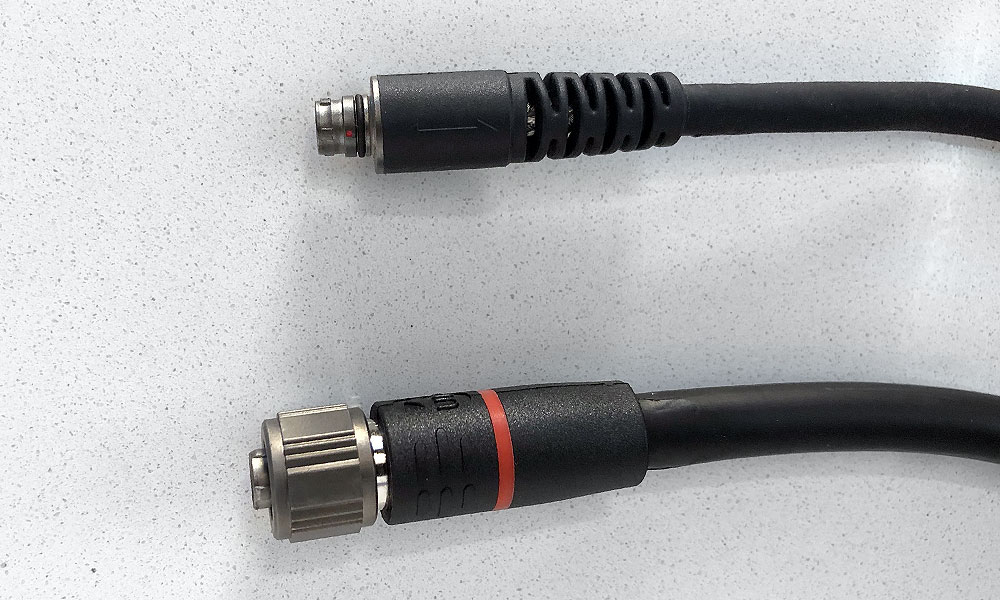
Bottom: New 26AWG cable (slightly thicker) with bayonet connector
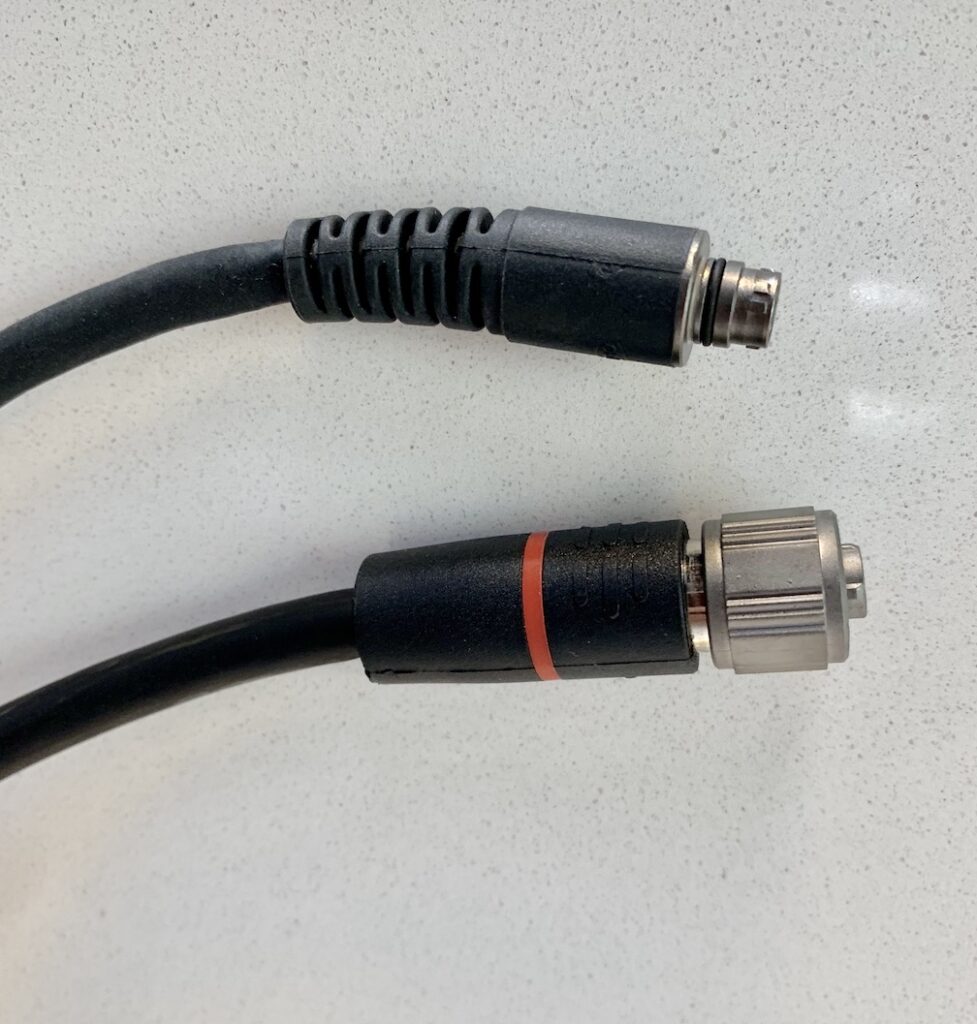
Bottom: New 28 AWG cable with bayonet connector
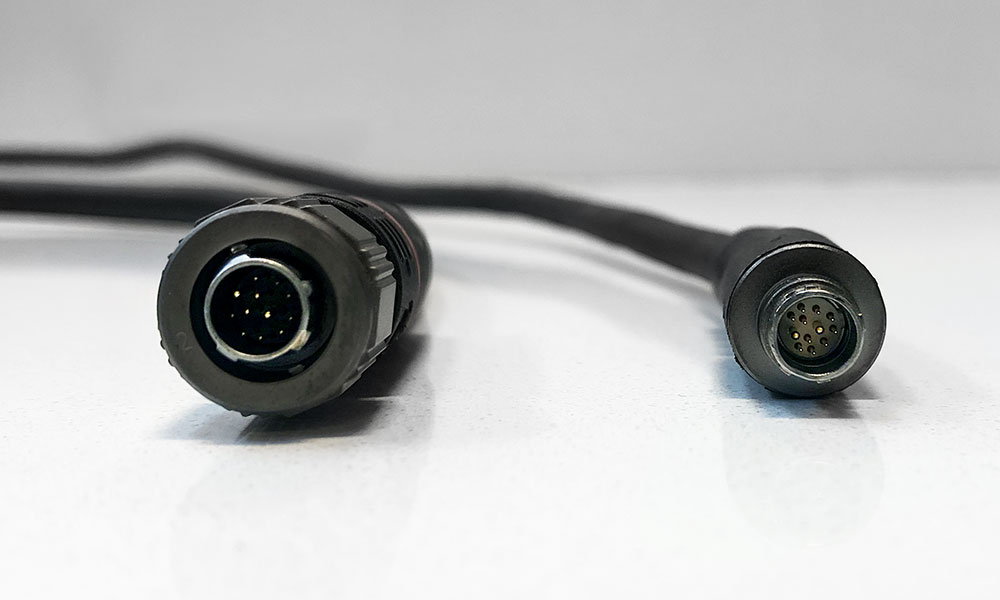
Right: Previous cable with push-pull connector
In addition, we’re offering our standard straight connector and finalizing tooling on a right angle connector. Straight connectors will remain the standard, but for applications where the lidar sensor needs to be mounted next to a wall or tight space, a right angle connector keeps the cable from protruding and generating gaps between the lidar sensor and other surfaces or components.
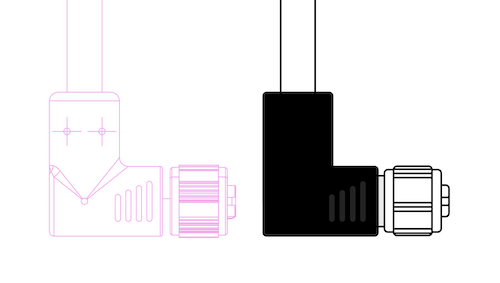
Finally, we’re giving customers the option to work with us and our cable supplier to design custom terminations. We’re making it easier for customers to get their preferred terminating connector, without having to spend time splicing it themselves. Reach out to discuss custom termination options.
Goodbye push-pull connectors
We’re planning to discontinue shipping sensors with push-pull connectors (and standalone push-pull connectors/cables/accessories) on July 31. Let us know before that if you have any unique needs with these connectors! And as always, we welcome feedback on our product developments and would love to hear your reliability stories.